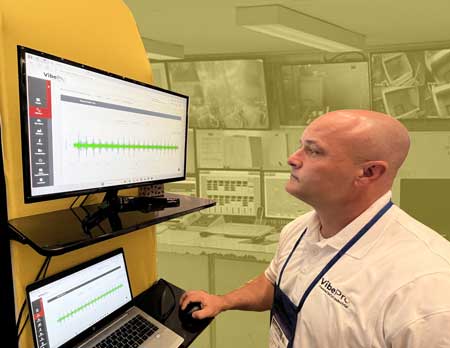
Predictive maintenance for manufacturing equipment has evolved over the years from a luxury to a necessity. Implementing a well-planned condition monitoring program allows operators to discover issues earlier on, before they grow into costly and catastrophic failures. Generally speaking, installing these systems and setting up the alerts is a pretty straightforward process. But the key to overall program success lies in the ability to effectively analyze the mountains of data that they generate. This requires specialized knowledge and expertise.
Plant operators find themselves faced with the old “make or buy” decision. They can either rely on in-house technicians for this critical function or outsource it to specialists. Today, we’ll look deeper into this decision and get a better understanding of the technical knowledge that is required to make condition monitoring truly effective.
The Technical “Basics” of Condition Monitoring
Before deciding on whether to build internal analysis capabilities or outsource them, it’s helpful to consider the key parameters that are measured. These include:
- Vibration Waveform – shows how the amplitude of vibration changes over time.
- Frequency – the number of vibration cycles per unit of time
- Amplitude – the magnitude or intensity of vibration, which indicates how much movement is occurring.
- Acceleration – the rate of change in velocity
- Velocity – the speed of vibration movement
It’s pretty easy to wrap your head around these parameters and their definitions. But that’s just the beginning. The challenge lies in truly understanding their impact and being able to correctly interpret them for each piece of equipment and its operating conditions.
Building Internal Predictive Maintenance Expertise
The make approach requires that operators build in-house capability. There are long-term benefits to this including institutional knowledge development, immediate access to analysis, and better integration with existing maintenance programs. Though in order to achieve in-house expertise, manufacturers must either hire capable technicians, or train existing team members. From our experience, yes, talented techs can be found, and people can certainly be trained. However, as skilled labor challenges persist, good help can still be hard to find. So the better alternative may be to train up. Though this takes time and money. And when we say time, we’re not just talking about the actual hours spent to learn the ins and outs, but the time it takes to develop experience. Further, you run that risk of losing people once they are trained. We’ve all heard or been through that story before – you invest in people, only to lose them to a competitor after they have mastered valuable in-demand skills. Even with these challenges, the make approach does work well for larger, high-volume operations that can benefit from the advantages mentioned earlier.
Outsourcing to Specialists
With the buy approach, manufacturers contract with third party companies that specialize in offering effective analysis services. This gives them immediate access to skilled experts without investing in training. It’s also the time-saving option, allowing techs to show up immediately or when needed. And these folks have likely worked in your industry before, as they typically have broader experience, across many industries.
Of course, there are drawbacks to this approach as well. Operators will pay ongoing service costs, which could add up over time. Control is also diminished which could lead to potential response time or availability issues since techs are in demand. Also, you might not always get the same person showing up, so there could be some learning curve involved with understanding a particular setup. Depending on the system you are running, if you are running a system such as VibePro, analysis can be done remotely, mitigating some of these drawbacks. Either way outsourcing is a great option for companies looking to ramp up quickly.
Making the Right Choice
Ultimately, the decision of whether to make or buy analysis services for a predictive maintenance program depends on several factors. These include company size, equipment criticality, budget, and long term strategies. In many cases, a hybrid approach can be the best way to go. Ramp up quickly with outsourced services, and gradually build your internal capabilities over time.
The importance of accurate analysis cannot be underestimated. Whether in-house or outsourced, the ability to correctly interpret vibration and other feedback transforms condition monitoring from a data collection exercise into an indispensable cost-saving tool.